Caution using the Close Holes button
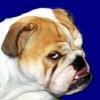
Sometimes when modeling I end up with a partial model that cannot be touched ... or even have it so that the face normal selector button can not be touched without crashing the program. Usually that's the end of that model as far as I'm concerned however the other day I did manage to trace the problem back to the "close holes" button.
I had a series of "holes" as in complete circle holes, the lines were all welded fine. I had manually clicked on each hole to have the close holes button close them. Went to lines and drew out a tessellation. Then any attempts to select faces, even for uvmap, and any attempts to select the face selector button up top ... anything to do with faces, crashed the program.
The solution for this one time was to go back to lines and by selecting the common line to each new face created by the close holes button, delete the lines. This effectively deleted the face normals and everything was working correctly once again.
I was able to repeat the problem even when the additional tessellation was not added. So the tessellation did not cause the problem.
Comments
Thanks for sharing!
This is one of those things that can really screw up your day after a long day's work :D
Hi Patience :)
Don't know if you were around when Afriname used to post here? He was a real sleuth in tracing problems with .obj's. He found that the reason for what you are describing is caused by twisted (non-planar) N-gons. These could well be caused by using the close tool. The only method that worked to get the file back was, strangely enough, to export it as .obj, open in DS and export out again as .obj.
Apparently DS's aversion to N-gons causes it to triangulate the N-gons, which fixes the problem. Import the .obj into Hex and you will be able to select the faces again and clean it up.
Be interesting for you to test this method, if you still have the file :)
typically I like to avoid the close holes feature except for simple things, especially when it comes to smoothing. Otherwise, I'll bridge it or close it up and then connect some lines across the closed area.
I find that the combination of UV domains and dynamic geometry smoothing functions are what causes crashes. When you remove the UV domains, a model becomes workable again.
I do and I shall give that a whirl and see what happens.
Same here - I only ever use it to check for holes, then abort and close by other means.
If it is the same problem that Patience is referring to; everything seems OK, but you can't even mouse over the mesh without Hex crashing.
Yeah, but this time there were so many holes to close, and to bridge every one I could not do without losing the precious uvmap which I wanted to maintain to match the other sides.
Tried washing the problem sides through D/S and "eventually" they loaded in Hexagon. One of the programs added a default mat with faces assigned to it.
Anyhow, for your amusement ...
and the rest ...
So, it did work, then:) I've never noticed that new option in Studio to triangulate N-gons - great idea.
Yes, using the close tool that way will definitely cause N-gons - Hex has no problem with that. It only becomes a problem when the N-gon is non-planar, which doesn't seem to be the problem here. From what you wrote in the third pic, it seems that you also had non manifold edges, which can really cause havoc!
It's a good idea to every now and then during the modelling process to have a quick run through what I call the diagnostic tools. Do a "select over-4-points faces", "select non manifold edges", "close" (just to see whether there are unwanted gaps - not to use it to fix gaps) and check on the normals - especially if you've used polyline tools to make shapes. These quick checks can save a lot of grief later.
Also a good idea to every now and then export the project as an .obj - just in case the .hxn gets corrupted, you can recover it through another app.
Materials being kept after deleting the object is quite normal - it happens in Carrara and other apps as well. Daz even introduced a function in Carrara a few iterations ago to purge unused materials, but this you have to do manually.
It is when you open a new blank scene and there are materials in it that you can start worrying :)
Since I don't know how to spot "non manifold anything ... okay ... will try that tip sometime and see what happens. ty
The comment about the polyline tools has me thinking back to another project that switched from using lines to returning to the basic cylinder shape for the clothing item. Don't recall atm what all happened, but yes, everything was not welded as expected shall we say.
from what I can see, there are far better ways to go about modeling such a shape more efficiently.
I should hope so ... please feel free to share the knowledge ;-)
Plates with tris which are low poly are not desired. And the only way I've found to keep the shape no matter how which programs apply smoothing, is to tessellate them to death.
well it depends on exactly what you're trying to achieve....whether it needs square edges or slightly rounded edges.
Non-manifold edges are those which have more than two faces attached. The highlighted face in my pic has non-manifold edges where the edges attach to the sides. This was done by first bridging those edges across, then bridging the edges from the top to the bottom.
Easy to do by mistake when you model in transparent mode, difficult to spot without using the "select non manifold" function.
missing pic?
I think I know what you mean though. I know if I have a closed section and want to attach it somehow elsewhere sometimes I have to first remove a face. Then after the action can replace the missing face.
Metal ... square edges.
Woops - old age catching up on me :)
it shouldn't be hard to comprehend what the process is in this image. it just mostly involves making sure you don't have any faces trapped inside one of the sections where they connect, and involves multiple copies of parts. And it actually has an extra line section in it, so it's not as efficient as it could be but still pretty efficient.
You can even make the corners and edges slightly rounded by selecting the proper lines in the proper order and doing a chamfer. All once must to is remove the top and bottom faces of the final shape, then close them up, select all the ringed lines at the corners of each square, chamfer those. Then select all the looped lines that make up the square shaped area and chamfer those too. Then you can just triangulate ngons on the closed faces.
When it comes to square metal grates and stuff, that may be better done with transparency and bump maps in most cases though.
Cute but when you add level 2 smoothing, those squares are going to be circular in shape. The corners would all need tessellating.
So will the sides ... think you're going to end up with something pretty close to what I had.
Well you said metal with square edges not rounded ones, which means you don't need to add smoothing to that method. And when I talked about chamfer's, that is basically just a form of controlled smoothing, so smoothing level functions are completely unnecessary after performing a proper chamfer.
Notice in the first image, all the edges have a slight roundness to them from the chamfer procedure.
But like I said, it's generally just best to use transparency and bump maps like in the second and third image. 1 face, far more efficient and soft on resources.
Let's not read too much into "what I mean" when talking about mesh modeling ;-)
The last image you posted looks fine except there are no holes in all those squares. Mind you if I can get that done and use one of the other options like symmetry or clone to make the reverse side, weld it together and it holds the square box shape [nothing inside the relatively sharp edged square] ... I shall look into trying chamfer a little more often. The times I have tried that have had very hit and miss results.
This is my process of going about chamfering edges. Always do the ringed ones first, then the top and bottom. If you do it the other way, it doesn't come out right or work at all..
Good tip, thanks :-)
........
edited ... you added more pictures! my last reply was made when there was only the 1st one showing.
Hope I'm misunderstanding - if you do a chamfer on the vertical edges first, then do the horizontal ones, you end up with some serious N-gons.
If you do the whole cube at once, it works nice and clean.
Those aren't ngons, they're no more than 4 sided except for the top face.
You can do both at once, but depending on the shape it may not work so well, and doing each separately gives you the opportunity to chamfer both at different levels and angles if desired.
Your example is just how it interacts with the outside surface of a simple cube, which doesn't really apply here even though they're similar. If I do both at once in a grate model scenario, you end up with this still, which is pretty imprecise when it comes to curves. You don't just get a rounded edge, you get slopes too.
Yes, I'm obviously referring the the N-gons this method causes on the top and bottom faces.
And yes, the shape and what you want to achieve will determine how you go about it. The shape you demonstarated was a cube, so I also used a cube.
I started with something like this.
I ran some tests using a more complex shape - see first pic. No1 was done using an "all at once" shamfer and No2 first the vertical then the horizontal. No1 gave me 10 N-gons and No2 16. What is more, trying to get the horizontal edges to be more rounded didn't work - it got to a certain point and wouldn't go any further.
The overall appearance of No2 is really bad - in smoothed shaded view there are ugly artifacts. No1 is clean and smooth.
Any attempt to select anything on No2 brought Hex crashing down - the same as what Patience reported in the start of this thread - and the N-gons aren't even twisted! No1 gives no problem in selecting and fixing N-gons.
My conclusion is that, excepting special cases where you want to have different parameters on different edges, or want to exclude certain edges from being chamfered, the "all at once" method is more efficient.
Not sure what you mean by "slope" - the roundness of the edges depends on what parameters are set, not on which method is used.
I had a go at finding a more efficient method of making the shape that Patience was having problems with and used the "all at once" method of chamfering without any problems. The mesh is clean and smooth, all quads except for the inside corners where I had to triangulate N-gons and there are no extraneous edges. See second pic.
Woops - the order of the pics has been switched :)