Adding to Cart…
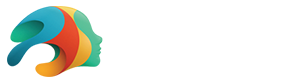
Licensing Agreement | Terms of Service | Privacy Policy | EULA
© 2025 Daz Productions Inc. All Rights Reserved.You currently have no notifications.
Licensing Agreement | Terms of Service | Privacy Policy | EULA
© 2025 Daz Productions Inc. All Rights Reserved.
Comments
How dose hair & clotes print do you have to chaing things
does ds print directly to the printer?
does mudbox?
like, what modeling software can print directly to the printer?
my dayjob bought a 3d printer. so excited. dunno what make and model yet
they deliberately torturing me. been begging for one for years lol
No
No
None that I'm aware of.
DS, and mudbox I assume, can produce OBJ files which then need to be run through a slicer program. That converts the OBJ file into g-code instructions for the 3d printer.
Get a good slicer as getting infill, supports and bases right will save you lots of filament and heartache from failed prints.
TBH I'm not a modeler and do all my printing from files produced by others. For me STL has always worked out better than OBJ but YMMV.
Also 3d printing is not one of those things where you can toss the manual and figure it out. Read your printers manual and find any tutorials you can online. Even very small issues can completely prevent the printer from producing useful prints.
if you are using an XYZ build up printer of any sort, the model needs to be put through a slicer, holes filled and supports added for overhanging mesh.
Resin this is not an issue
don't ever buy a DRM protected printer like me!
even buying the genuine filament it did not identify the built in chip in the cartridge and won't work and their customer service basically told me to sod off
eeeeeeeew taking a move right out of crappy regular printer playbooks :(
what software has slicer?
Thaks.
they bought a Creality3D Ender-3 Printer
is this good? https://slic3r.org/
Meshlab and Cura are both free, good, easy to use, and work well with the Ender-3 (my son uses Cura a lot with his Ender-3).
I recently purchased a Creality FG 3d resin printer. This is a (bad) photo of the Bullywug converted to a 28mm scale figure printed for an upcoming game. The details are quite good.
1) Posed in DAZ Studio exported as .obj
2) Imported to Blender, it's considered a bunch of pieces, which I joined,
3) Using 3D-Print tools (part of Blender, but you have to turn them on first) Clean up > Make Manifold and export as .stl
4) Bring into Chitubox (slicer that comes with a lot of resin printers) and scale against another figure. Add supports and print.
The second figure I had to add weight to the cloak (Solidify) because it was one plane thick.
-- dup post --
I used Meshlab when I had a filament printer. I quite liked it.
My resin printer came with an absolutely awful slicer and I got Chitubox and think very highly of it.
thank you for the steps!
the first thing they want me to make is custom keyboard caps for a 104 keyboard
they want to block some keys from being pressed
its the back of the key is tricky cuz it has to secure on to the peg. its a very precise measureent
i'd like to print some shrubbery for my christmas village.
and a miniature of an aviation headset with mic boom to make cute carm bracelet charms. my dayjob does air to ground communications.
what does g mean in g coordinates?
This is straying pretty far from DS but here goes.
If you can 3d model then you should be able to make the custom keycaps pretty easily. You can easily enough find keycap STL files, and lots of other stuff, at thingiverse as well. But you'd need to add the stop yourself.
I hope you're going to be doing it to a more regular keyboard and not that Model M.
Shrubbery is easy. Find a model you like, from your Daz assets, thingiverse or one you model yourself (keep in mind that the mini will be small so don't go crazy on detail). Same with the headset. Once you have either an OBJ or STL file feed it into your slicer and put the resulting g-code file into your printer. The printer will have either an ethernet connection or an sd card reader expressly for that. From what I could find it appears to have bopth, or possibly wifi it wasn't 100% clear. Every printer I've ever seen has an sd card reader so that is how I do things as it lets me put the printer out in the garage rather than somewhere the fumes will be an issue.
I assume g coordinates is actually g-code coordinates. g-code is a family of related programming languages used in CNC devices, including 3d printers. What the g stands for I have no idea and a few minutes on Google didn't turn anything up. The coordinates are in 1 mm increments.
That's a Unicomp. I have two Model M's that are still working perfectly, with USB adapters, after almost 35 years. My Unicomp was half the weigth and while I was briefly in buckling spring heaven on every computer I use, it crapped out after two months, as did the replacement. I hear they recently abandoned the replaceable keycaps as well. Incredible how badly Unicomp could misunderstand their customers: People who would search and search and spend $400 bucks on a relic because of the quality are not interested in you shaving pennies off the price and delivering cheap garbage for $94.
Sorry for the rant, but I've never been so first excited and then dissappointed in a company and product.
the replaceable key caps is a big issue at day job. the operators are used to the exrra wide key. the 104 they buying now is 2 indiviual keys. makes the operators upset.
they recycling the old keycaps from the rs6000 days 20 years.
tee hee
Boba Fett Helmet Keycap
I'm a kb snop too. I've had better luck with unicomp, I did buy from them right when they started. I have heard quality has dropped off.
I just used Model M as the generic term.
I've had really no luck exporting models out of DS straight into my slicer. There are always printing problems. It is obvious to me that there needs to be an intermediate step to do something. I'm not sure what.
It would be so cool to be ale to print your creations in DS.
What settings are you using in the slicer? Are you adding supports?
yes..supports, its mainly turns to stringing, holes, etc. The print has holes it what I mean.
Is there any chance you could describe the process you go through, step by step.
First off, I assume you export .obj, and opening in the slicer.
Does the figure have clothing? If it does, that can be a source of problems. Most DS clothing is surfaces with no thickness, which does not print well, giving holes or disconnected areas. Exactly how it manifests itself will depend on whether the printer is a wire or resin type and the slicer response to thin surfaces. I have started to write a program to deal with that, but have only tested it once on my printer (an Anycubic Photon) before my allergy to the resin stopped my using it stone dead, and my interest in verifying the program waned a bit.
Have you tried converting to .STL as an intermediate step? If not, and you don't have one, I wrote a Windows program for myself to do that and it's a freebie here: http://www.chestnutpens.co.uk/misc/objtostl.html. Put the .STL through the slicer, may give a more complete model. Obj files straight into slicers is moderately new and yours may not be bug free. Then if it still goes wrong, could you post a photo? Someone may recognise the problems and help or at least come up with plausible options to try. If not.. it'll make the rest of us feel better because we're not the worst off.
Stringing can be caused by a number of factors. Did you level the printer? You need to put the printer on as level a surface as possible and then do the leveling process for the printer.
But holes means the geometry isn't right. If you read back over the thread someone details how they take their DS OBJ into blender and close up the holes in the geometry.
Sorry for hijacking the topic a little but, last off topic post.
I love buckling springs so much that I was going to buy a third one and hope for the best. When I returned to the site, I found something called the "New Model M", supposedly with better QC and keycaps. After reading some positive reviews, I of course couldn't resist. I'll let you know how it works out.
Oh well. My "New Model M" just arrived. True, it seems sturdier, the switches are a dream, but it no longer has detachable keycaps and the Scroll Lock LED doesn't illuminate. Of the three keyboards that I've bought from them, two stopped working within three months, and the third was deffective on arrival. We'll see how long this one lasts.
Well crap. Mine is pretty clearly on its last legs. I have a Corsair with Cherry blues at work I like well enough but it will be sad day when buckling springs go away.
this the one i ended up with
https://www.amazon.com/Official-Creality-Flexible-Comparable-220x220x250mm/dp/B094FPHKW7
havent printed on it yet. looking for a boeing b17 model to print on it.
A good, solid little printer, should do the job.
-- Walt Sterdan
The mouth is a likely source of holes, the cheeks are too thin to print, at least that's my experiance. On the prints i have done so far I remove the eyelashes and then used UVmapper to delete the materials of the mouth and teeth ( that deletes the mesh for those parts ) then I put the model through Meshmixer and seal all the holes. I haven't found a way to print hair, I think it needs to be a solid hair shaped blob to print hair.. Ears and fingers can also be a problem if the scale of the print puts them below the printer resolution.
Has any one tride lost PLA metal casting there prints. I'm not good at painting so I thought this might be an option.
I woud like to do gebesis 2 cosplay Rory Mercury poll dansing around Santi Guterez sorry I'm a otaku
a 1/7 PVC figure is US $664.61
I picked up one (B-17) in the Daz store that was sort of ok. The trick seems to be to search for WARPLANE instead of keywords like aeroplane and aircraft.
The discussion about the resins and the fumes and ventilation kind of reminds me of PVC clays like Fimo and Sculpey. You bake those in an oven and they shrink a tiny bit, and become fairly durable.
So I assume that when the resin has cured or has otherwise settled down, the smell or any off-gassing dies down as well? And hopefully the printed surface will take a good quality, durable paint like Testors or Humbrol, Polly S etc. Or do you need a cleaning agent like Polly S Prep say.
P.S. Glancing at the Wikipedia English entry for Fimo mentions "issues"... ergo the article says "you can slice it after it hardens"... I'm thinking that may be possible but you'd need an X-Acto saw or a Dremel tool, and I wouldn't want to breathe in the dust!! However the Wikipedia item reminded me that soft PVC clay will indeed slice *VERY* thin with an Olfa or Stanley knife, possibly thin enough to make Geoshell-like, physical layers of durable color that could be glued to various surfaces of 3D printed, resin objects. On the down side I think thin slices of Fimo are hard to bake. But you could add nicely sculpted items of clothing, made out of Fimo, to a 3D "printed base" action figure. Like a gown or a leather jerkin or a belt and buckle around the waist that is really "3D".
I wonder if these printers will do a negative printout? Then you'd have a nifty mould and with some tweaking, a reproducible action figure - press bits of Fimo (in appropriate colors) into the mould and then bake the pieces of clay and assemble the figure. Just saying.
And if you could 3D print in beeswax or paraffin or a similar substance then bingo - here we go with lost wax castings!
Attached, a sample object made out of Fimo and varnished with clear and white acrylics. Point being that a fine artist's brush can supply surface detailing that the 3D printed resin can't quite match.
With my Anycubic Photon DLP printer on a 90mm high figure I was able to see the fingernails and the ties on the hips of the bikini bottoms. DLP printers, at least, can do incredibly fine models. On the one photographed, there was a bit of delamination in the base, which is why I added the filler. The head height is approx 12mm (1/2") to give a sense of scale.