Adding to Cart…
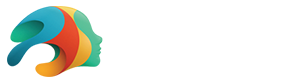
Licensing Agreement | Terms of Service | Privacy Policy | EULA
© 2025 Daz Productions Inc. All Rights Reserved.You currently have no notifications.
Licensing Agreement | Terms of Service | Privacy Policy | EULA
© 2025 Daz Productions Inc. All Rights Reserved.
Comments
Wow, the hair looks kind of good for a figurine of that size. The Royal Doulton (fine china) people must be nervous!
I hope people will post about the paint issue - what kind to use, durability etc. And whether my idea about making some clothing and accessory bits out of PVC (or casting the entire figure, in colored PVC, from a 3D printed mould) is of any value.
i just ordered a Prusa i3 MK3S+ . I've read a ton about it and it seems to print pretty well will good results overall, less fiddling around. Yes, the tech is a bit old, but if it works like I want, it will be worth it.
It would be great if someone could post the step by step to making DAZ models > exported as obj work for 3D printing. I did send one over to Gameprint, but I don;t want to spend that moeny for every model. It worked but I didn;t think all that well.
I've got a figure that I'd love to print. But the hairstyle that I use for her is Perrin Hair: https://www.daz3d.com/perrin-hair-for-genesis-3-8-female-s
Can anyone guess if a 3D printer would be able to print this hairstyle, or will I have to find something else (I'm thinking about the supports that may need to be added)?
+1
I had an elegoo Mars 2 pro, a resin printer. I used water based resin. From start to finish I felt that the printer was very easy to work with and clean. I paid around 425 - 450 bucks for the printer, a curing station, some tools and extra plastic. So not all that terrible price-wise. I really enjoyed the quality of the model that it produced. It didnt take long to make it either.
One day , I was working on the model, triming the excess plastic from the models hair. I slipped with my exacto knife and cut off a portion of the models face and hair which ruined the print. I looked at the damage, and wondered what it would take to repair the damage. And then I realized how much time I was spending on the figure. I placed it in the plam of my hand and with appropriate force, crushed the print into many small peices which ended up in the trash. That was the first and last time I ever used the printer. It made its way over to my father in laws house, who has subsiquintly never used it since.
What you need to really consider is what you want the printer for and what level of quality you want from the prints. I wanted to make 1/35th scale figures using daz models. Over all, not difficult to prepare for printing. The hair on the other hand took alot of time in modelling programs trying to get it more or less print freindly. The hair conversion actually took the most time in the whole process. Considering that I wanted to make intricate scenes with several figures, I was looking at alot of time in just getting models prepared for print. Also, remember that you have to support the models in your preffered 3d print program by making a sort of scaffolding for them. I forget what that process is called exactly but it can also take a good amount of time depending on the models detail. Alot of printing software have "Auto" functions for preperation but they may or may not provide the best solution for your project. There are some companies out there that will prepare your print for you for just a couple dollars. I found that it was unneccesary to use these services as I was able to get better results than they could offer with just a bit more time using free 3d print software.
Im also kind of a perfectionist though. As far as my hobbies go, I can get pretty fussy if something isnt turning out specifically as I imagine it. If this isnt a concern for you then maybe my experience wont apply to yours. I would just be sure about what it is you want from a 3d printer and how much work you are willing to do to get the final result. Also, do some research so you know what is involved.
IMPORTANT! Research the best way to clean the printer and its components. Very important to avoid damaging the product.
somewhere along the line I saw one of the programs have a command called "make solid" which could help in the hair dept. I think.
Yah, make solid was very useful when prepping the model. I didnt have alot of luck using it with hair though. I was very new at it though so, maybe? The whole time I was working with it, I just wanted to render. :)
I'm rea writing this post because I don't think I explain my self . My sister is also an otarko & would like to collect the figurines but they are very expensive & her grandchildren are autistic. My nephew is a dungeon master in D&D & would like figurines of his creation So has any one done lost pla casting. I have dyslexia this post has taken me 4 hours to write so I would like an answer
I can give part of an answer. If you are wanting to cast the usual 28-35mm high Warhammer type D&D figures, then
Lost PLA will not be suitable.
The filament printers do not give adequate resolution for that. The only type that do at a size that small are the DLP printers.
If the figure is to be 150mm (6") or above, then lost PLA should work, but I have not tried it.
If the figure is around 100mm (4"), Lost PLA will probably do a job, but it may be a bit disappointing.
Regards,
Richard
I have found this product WAX Castable Resin
Hmmm... a few different manufacturers, several videos too! One (chosen by me at random) says "PowerResins WAX is a special wax castable resin for 3d printers (sic) that is very similar to wax. It is used for jewelry casting and most specifically for models with stone settings and surface models."
Not sure what a "surface" model is but it seems that with this you are indeed starting with a 3D modelling software (DAZ's Hexagon, DAZ Studio, DAZ store content, Blender etc.) and from there you go to something like wax, for casting in hot metal (hopefully gold, not lead heh) in a foundry.
(Edit) Here is an example of a foundry that paid Google to be positioned high in search results. Just chosen at random by me but if you scroll through the page you'll learn a bit about industrial casting starting with "a few grams" (sic) of aluminum. And down towards the bottom - yeppers, they have upgraded to 3D printing for a variety of reasons/applications. This part of the page is so recent that it still had typos in the autumn of 2021!
Related: I have long been fascinated by a guy named Gord Hoselton who makes artwork out of essentially beer cans. (Notice how the above foundry uses only "cerfified" ingots).
Anyway, one morning about 30 years ago probably, Hoselton took a reporter on a tour during a radio program. I was fast asleep but I could hear the radio, so in my mind I had this sort of semi-lucid "virtual tour" which went as far as him picking up bits of scrap from the shop floor as he walked through his place, and he'd toss the stuff into molten vats and I was recoilling from the arc of the splashes - woah! Keep that stuff away from me!!! sort of thing.
Since it's clear the guy is still in business (http://www.hoseltons.com/index.php/sculptured-gifts-collectibles/ornaments/) I'm going to send him a snail letter to find out what the average commissioned casting costs. I have an idea for something in the action figures or "Hollywood pre-production maquette" category and it requires small blocks of molten aluminum. Good project for someone who is familiar with lost wax; some skill with Genesis 8 and "Dog 8" would be valuable as well.
Thanks, diron_di... 8da8 !
This bloke explanes it well